THIS SERVICE IS CERTIFIED TO MEET THESE REQUIREMENTS
*Not a complete listing of available specs. Contact us at 763-373-7533 or email us at [email protected] for review and confirmation of your specification or to request a quote
USA Specifications
NADCAP Specifications
- AMS-C-26074
- MIL-C-26074
- AMS 2404
- ASTM B733
- 580-5296-001
- 580-0766-001
- 580-0766-002
NON-NADCAP Specifications
- 9902106
- ES10006
- M695215
Mexico Specifications
NADCAP Specifications
- AMS-C-26074
- MIL-C-26074
- AMS 2404
- ASTM B733
NON-NADCAP Specifications
Specifications not Supported.
MEDIUM PHOSPHORUS ELECTROLESS NICKEL PLATING
Medium phosphorus (Mid Phos) electroless nickel is ideal for applications requiring a uniform plating where magnetism is acceptable.
-
Moderate Corrosion Resistance
-
65 mΩ/cm Electrical Resistance
-
Mixed Crystalline / Amorphous
-
Direct Plating on Ferrous Metals
-
5-9% Phosphorus Content
-
1000ºC Melting Point
-
.83 Friction Coefficient
-
8.1 G/cm³ Density
-
0.7% Ductility
-
Magnetic
-
Solderable
-
Uniform
-
Semi-Bright / Bright
-
Aluminum
-
Steel
-
Stainless Steel
-
Bronze
-
Copper
-
Brass
-
Super Alloy
HIGH PHOSPHORUS ELECTROLESS NICKEL PLATING
High phos electroless nickel is ideal for heavy-build applications but is inherently less hard than medium phosphorus electroless nickel. Performing a heat treatment can enhance the deposit durability.
-
Excellent Corrosion Resistance
-
100 mΩ/cm Electrical Resistance
-
Direct Plating on Ferrous Metals
-
10+% Phosphorus Content
-
880ºC Melting Point
-
.45 Friction Coefficient
-
7.8 G/cm³ Density
-
1.50% Ductility
-
Non-Magnetic
-
Solderable
-
Amorphous
-
Semi-Bright / Bright
-
Aluminum
-
Steel
-
Stainless Steel
-
Bronze
-
Copper
-
Brass
-
Super Alloy
ELECTROLESS VS ELECTROLYTIC NICKEL PLATING
Standard nickel plating is an electrolytic process while electroless plating is autocatalytic, meaning no external power supply is required to apply the deposit. A part receiving electroless plating will continue to build a metal deposit so long it is in the tank. This creates a uniform plating with a standard deviation around +/- 0.00001”. Electrolytic plating requires an externally applied DC current, which potentially leads to a non-uniform application near the corners and edges of a part.
Electroless plating reduces ductility, so applications that require high ductility are better suited to the electrolytic process. Additionally, electroless nickel plating is not ideal for applications that demand high heat resistance.
ELECTROLYTIC NICKEL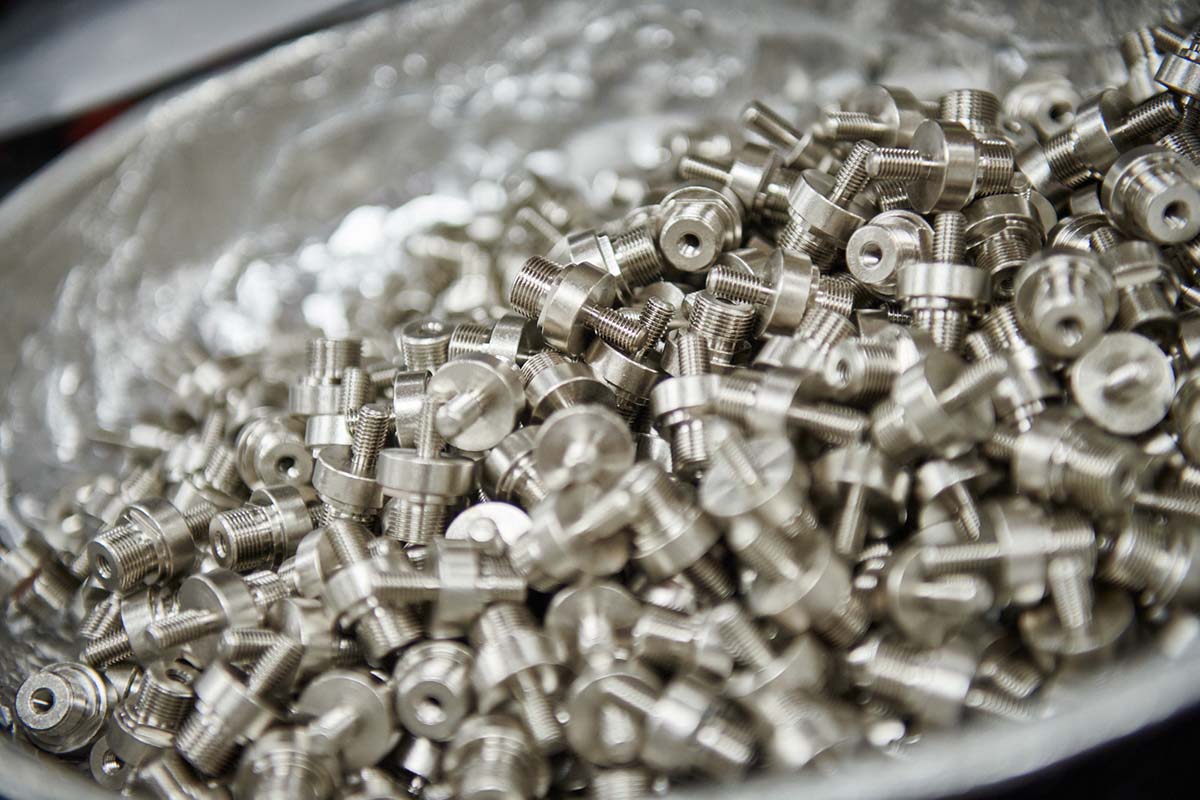
APPLICABLE INDUSTRIES
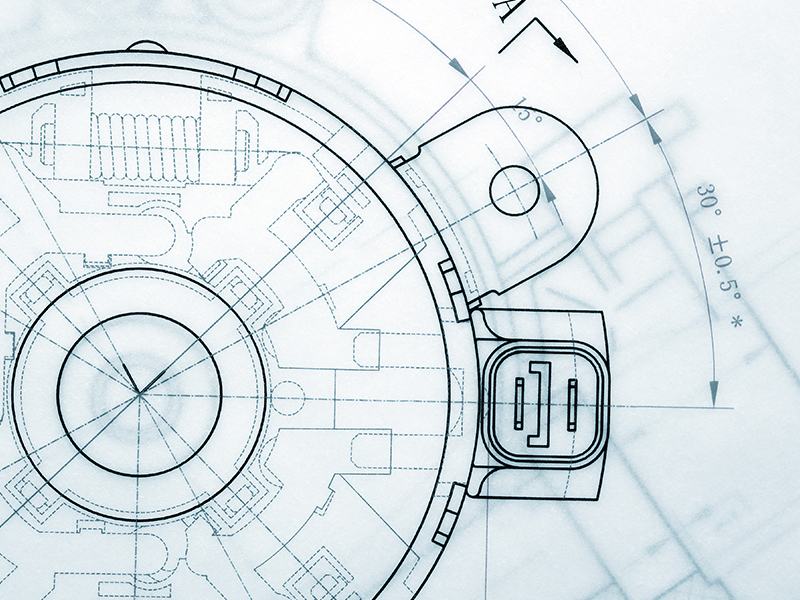